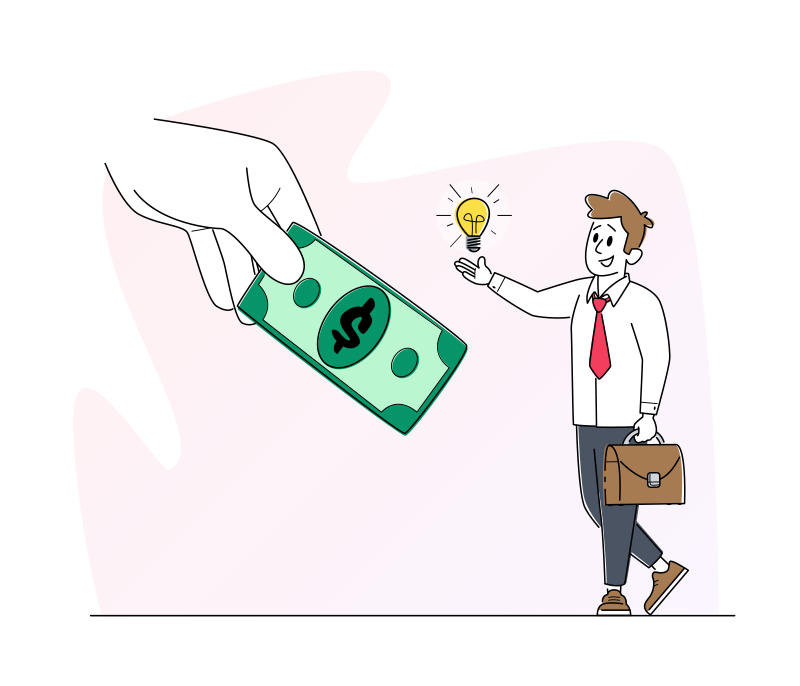
5 Tips to Save Money by Effectively Managing Equipment Inventory
Assetbots Team
Your organization’s equipment inventory is an essential part of your business and a significant investment. When you think of each asset you own, and the cost to acquire that asset, the number quickly adds up.
If you are in an office environment, the equipment you provide to each employee (e.g., computer, keyboard, mouse, headset) can easily exceed $1,000 USD. If you have 50 employees, that’s $50,000 USD worth of assets right there. If this were $50,000 USD in cash, would you be tracking it and trying to figure out where it came from and where it’s going? Of course you would.
The same should hold true for your equipment. Your equipment holds value and is an asset of your organization. It is equivalent to money. If you are not effectively managing your equipment, you are not doing a full accounting of your finances.
Apart from the monetary loss an organization might have as a result of equipment loss or theft, failing to effectively manage equipment has other costs in terms of productivity and time wasted when dealing with equipment purchases, tracking, and repairs. Your employees don’t want to waste precious working hours trying to track down equipment they need to do their job. Your organization shouldn’t be wasting money purchasing equipment when you already have unused or underused surplus equipment of the same type tucked away in a warehouse or storage room.
Read on for tips on how to effectively manage your equipment inventory, and how doing so will save your organization time and money and help prevent asset loss and theft. Although each of these tips on its own will be helpful to your organization, following all of them will have the greatest impact on your organization’s finances and productivity.
1. Make an Equipment Inventory List
The first step in effectively managing your assets is knowing what you have. You may have a general idea of what you own, but once you put pen to paper and track each and every asset, you will be surprised at the combined value of all of your assets.
Your equipment inventory list should include every asset you own and some basic information about each asset such as its value, location, and condition. As you retire assets and purchase new ones, you should make sure you are always updating your inventory list.
Although this step may seem labor-intensive, knowing what you have and where it's located is the most effective way to prevent asset loss and theft, and to save the organization time and money when tracking down assets or making purchasing decisions.
2. Track Usage of Your Equipment
After you have figured out what assets you have, you should then determine how those assets are being used. Find out who is using those assets and how often. Are they assigned to one specific person or shared among users? Are they used on a daily basis or infrequently? Where is the equipment being used? In a remote location or in the office? The answers to these questions will help guide the organization in making decisions about equipment management and purchasing.
For example, you might find that you have a shortage of headsets in one location, and a surplus of headsets in another location. Knowing this detail will prevent you from making unnecessary purchases and allow you to better prioritize your spending on things your organization actually needs.
Or you might find that you have some types of equipment that no one is using anymore. In this case, it might be best for the organization to sell or recycle that equipment. Doing so can bring money back to the organization and prevent a situation where equipment is left collecting dust and losing value in a storage area.
3. Regularly Maintain Your Equipment
To maximize the lifecycle of your equipment, all maintenance schedules should be proactively maintained. Knowing what condition your equipment is in and what needs to be done to keep your equipment fully functional will go a long way toward saving your organization time and money. For example, proactively maintaining equipment will minimize the time your organization spends dealing with repairing equipment that has broken down. Since you know how often the equipment is being used and who is using it, you can schedule maintenance based on need in order to make optimal use of your organization’s time.
Additionally, unscheduled repairs can negatively affect employee productivity, which also results in costs to an organization. By having an inventory of your equipment, repairing equipment becomes easier to do. You now know where you may have spare parts to facilitate repairs and whether you have available loaner equipment for the impacted employee or department.
Finally, there are situations where equipment simply cannot be repaired or has reached the end of its life. Some equipment, particularly IT equipment, retains value and can be sold even after it has reached its end of life. There are IT asset disposition companies and recyclers, like Dispoteca, that will pay you for your old and surplus equipment and will coordinate picking up the equipment from your offices. Knowing when your equipment will be reaching the end of life will help your organization maximize the resale value of your equipment if you choose to sell or recycle it.
4. Look for Trends
Now that you have a complete picture of your equipment and how it is used, you can look for trends to guide your decision making and planning. Does one employee tend to request more repairs than others? Perhaps training is needed for the employee on how to properly care for the equipment.
Do certain brands of equipment tend to break more frequently than other brands? You might take this into consideration when making your next purchase.
Do employees show a preference for using some types of equipment over other types? This information might influence your purchasing decisions in the future. Or if employees are shying away from using newly-introduced equipment, this might be an organization’s cue that more training on new equipment is needed.
5. Use an Equipment Inventory System
You are probably paying for accounting software to help you manage your finances. Equipment inventory software can bring your organization just as many benefits as accounting software in terms of loss prevention, resources management and productivity gains. Additionally, asset tracking software can assist you in avoiding discrepancies in audits, taxes, and maintenance fees, which can help reduce your compliance risks and tax liability.
Although you can track your equipment inventory by hand or on Excel spreadsheets, doing so can get cumbersome and time-consuming, and suffers from limited functionality. Asset tracking software can help you implement an efficient and effective equipment inventory system quickly and accurately.
Assetbots is easy-to-use, modern asset tracking software that is cloud-based and can be accessed from any internet-enabled device. Among other features, Assetbots allows you to quickly and easily:
- Compile an inventory of your equipment
- Track usage and location of your equipment
- Schedule maintenance and reserve equipment for other uses
- Check-in and check-out equipment from any internet-enabled device
- Store all warranty, contract and instruction manuals for equipment
- Create reports about your assets to analyze factors such as history, value, and usage
Assetbots is currently offering a limited number of free subscriptions. Visit www.assetbots.com to reserve your free subscription and start minimizing your organization’s asset losses and unnecessary purchases. Start tracking assets today!